Xem thêm: Hướng dẫn quy trình kiểm tra chất lượng vải theo hệ thống kiểm tra 4 điểm
Xem thêm: Máy kiểm vải tự động ở đây
Xem thêm: Lợi ích của máy kiểm vải tự động so với kiểm vải thủ công
1. Horizontal lines (Đường kẻ ngang)
-
Nguyên nhân:
Thường được gây ra bởi:
- Lỗi trong ống cuộn (thùng dùng để giữ sợi)
- Độ căng sợi không đều
-
Cách phòng ngừa:
Thay ống cuộn định kỳ và kiểm tra, điều chỉnh độ căng cũng như vị trí của sợi thường xuyên.
2. Shade variation (Biến đổi màu sắc)
-
Nguyên nhân:
Gây ra bởi:
- Sự trộn lẫn của các loại vải được sử dụng trong sản xuất
- Các biến đổi trong quy trình sản xuất liên quan đến thời gian và tốc độ
- Việc cắt, đóng gói và/hoặc đánh số không đúng cách
- Sự giãn vải không đồng đều
-
Cách phòng ngừa:
Sử dụng cùng một nguyên liệu cơ bản và bộ tham số nhất định cho mỗi lô sản xuất có thể ngăn chặn hiện tượng này. Khi đến thăm nhà máy sản xuất vải thô, cần đảm bảo công nhân chỉ kết hợp các sản phẩm cùng màu và thực hiện quy trình cắt, đóng gói đúng cách. Việc đánh số chính xác sẽ giúp ngăn nhầm lẫn giữa các mảnh có sắc độ khác nhau.
3. Dirt/stains (Bẩn/dây màu)
-
Nguyên nhân:
Có thể xuất hiện từ:
- Bụi bẩn từ sàn nhà máy
- Dầu mỡ từ máy móc
- Thuốc nhuộm
-
Cách phòng ngừa:
Làm sạch máy móc và thiết bị định kỳ để đảm bảo không có dầu, mỡ hay thuốc nhuộm ngẫu nhiên dính lên vải. Bọc các cuộn vải hoàn thiện trong màng nhựa và lưu trữ ở khu vực riêng biệt, cách xa khu vực nhuộm.
4. Uneven dyeing/printing/dye marks (Nhuộm/In ấn không đều / vết nhuộm)
5. Drop stitches (Mũi thừa)
6. Misprinting, off printing or absence of printing (In sai, in lệch hoặc thiếu in)
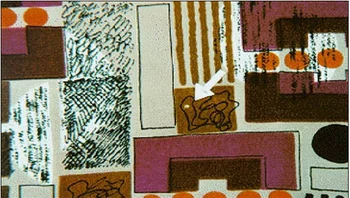
7. Crease marks (Vết nhăn)
-
Định nghĩa:
Là những vết biến dạng có thể nhìn thấy trên vải, không giống như vết gấp kéo dài trên toàn cuộn mà chỉ xuất hiện ở một điểm cụ thể. Nếu quá trình ép cuối cùng không khôi phục được, vết nhăn sẽ còn lại và có thể kèm theo sự mất màu.
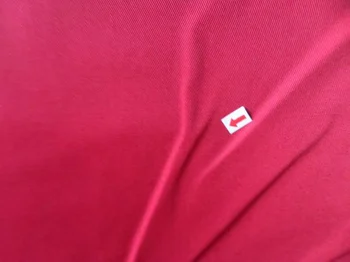
-
Nguyên nhân:
- Chuẩn bị, thư giãn hoặc phồng vải không đầy đủ
- Vải có cấu trúc chặt, sợi xoắn cao hoặc trọng lượng dày đặc
- Máy không phù hợp với việc xử lý các nếp gấp
- Nạp vải không đúng cách dẫn đến dây bị xoắn hoặc bị nút
- Tốc độ làm nóng hoặc làm mát quá nhanh
-
Cách phòng ngừa:
Sử dụng chất chống nhăn trong quá trình giặt sạch trước khi nhuộm và xử lý cẩn thận quá trình ép vải.
8. Barre (Barre)
-
Định nghĩa:
Là mẫu hình thị giác lặp lại của các thanh hoặc sọc liên tục chạy ngang qua vải, thường xuất hiện dưới dạng vệt ngang của các thanh sáng hoặc tối chạy qua chiều rộng. Các thanh này phải xuất hiện theo một mẫu lặp lại và thường nằm song song với hướng chảy của sợi trong vải dệt hoặc các hàng của vải đan tròn. Thường chỉ được phát hiện sau khi quá trình sản xuất kết thúc.
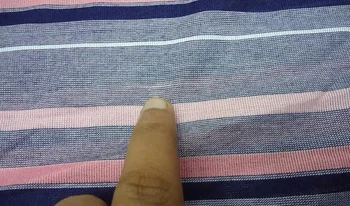
-
Nguyên nhân:
Do sự khác biệt về vật lý, quang học hoặc thuốc nhuộm giữa các sợi hoặc do sự khác biệt hình học trong cấu trúc vải.
-
Cách phòng ngừa:
Duy trì sự nhất quán trong tổ chức và dán nhãn nguyên liệu thô, kết hợp với bảo trì thiết bị liên tục và áp dụng hệ thống hàng tồn kho FIFO để hạn chế lỗi này.
9. Neps/knots (Vết xơ/Nút thắt)
-
Định nghĩa:
Là những khối sợi nhỏ, chặt chẽ bị rối theo hình dạng của đầu kim, thường bao gồm các sợi chết hoặc sợi non.
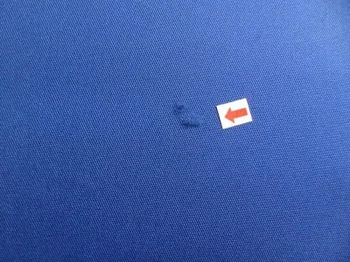
-
Nguyên nhân:
Có thể phân loại thành:
- Biological: Xuất hiện trong nguyên liệu thô, chứa mảnh vỏ hạt, lá hoặc thân cây (loại bỏ qua xử lý ướt).
- Mechanical: Xuất hiện trong bông đã qua xử lý, mảnh sợi do quá trình cơ học.
- White speck neps: Chứa cụm sợi non, thường không nhìn thấy cho đến khi nhuộm và được coi là nghiêm trọng nhất.
Nguyên nhân chung là do các cuộn sợi bị buộc lại, có thể do sự tích tụ của ruồi và mảnh vụn trên máy móc, vệ sinh bông không đạt chuẩn, và quá trình chải không loại bỏ hết neps.
-
Cách phòng ngừa:
Đảm bảo bảo trì và làm sạch máy móc, các bộ làm sạch con lăn và loại bỏ sớm neps qua quá trình chải trước khi xử lý.
10. Abrasion marks (Vết mòn do ma sát)
-
Định nghĩa:
Là những vùng đổi màu trên vải do bị hư hỏng bởi ma sát hoặc cọ xát; đôi khi còn được gọi là chafe marks hoặc chỗ bị bầm.
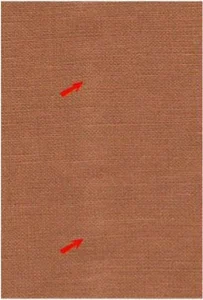
-
Nguyên nhân:
Do va chạm hoặc cọ xát với bề mặt cứng, thô (ví dụ: vết trầy trên breast beam của máy dệt) và khả năng chịu mài mòn của vải phụ thuộc vào đặc tính của sợi, chỉ và quá trình hoàn thiện.
-
Cách phòng ngừa:
Sử dụng các loại vải có khả năng chịu mài mòn cao (ví dụ: Nylon, sau đó là Polyester) để giảm thiểu lỗi này.
11. Splicing (Lỗi nối vải)
-
Định nghĩa:
Là việc chồng lên nhau các đầu cắt của hai mảnh vải (đầu của một đoạn và đầu của đoạn tiếp theo) nhằm đảm bảo việc trải vải liên tục.
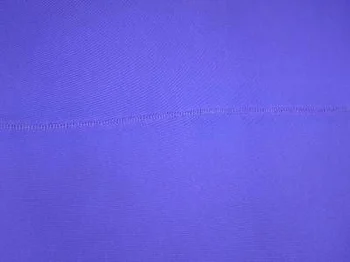
-
Nguyên nhân:
Các đầu vải chồng lên nhau tạo ra chất thải trong quá trình sản xuất; tổn thất do splicing có thể lên đến 5% tổng lượng vải. Vị trí của splice trong cuộn vải thường phụ thuộc vào chất lượng tổng thể của vải và được sử dụng để bù đắp các khuyết điểm khác như vết bẩn hay lỗ hổng.
-
Cách phòng ngừa:
Cải thiện chất lượng tổng thể của vải và ngăn chặn các khuyết điểm khác, đồng thời thiết lập giới hạn dung sai cho splicing (ví dụ: không quá 1 splice mỗi 30 mét) với nhà cung cấp.
12. Holes ( thủng lỗ)
-
Định nghĩa:
Là khuyết điểm xảy ra khi một hoặc nhiều sợi bị hư hỏng đến mức tạo ra một khoảng trống trên vải.
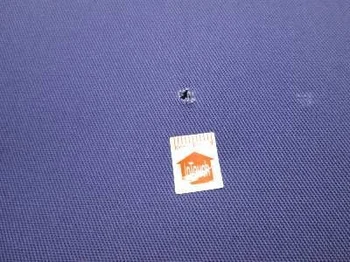
-
Nguyên nhân:
Thường do một vết cắt hoặc rách không chủ ý, với kim gãy hoặc bộ phận máy móc thô ráp là nguyên nhân phổ biến.
-
Cách phòng ngừa:
Đảm bảo nhà cung cấp có quy trình kiểm tra kim và máy móc định kỳ trước khi sản xuất.
13. Defective selvage (cut, waved or creased) (Lỗi biên vải– cắt, gợn sóng hoặc nhăn)
-
Định nghĩa:
Selvage (biên vải) là phần mép dệt chặt của một mảnh vải, giúp ngăn vải bị bung hoặc rách. Lỗi này có thể xuất hiện ở dạng bị cắt, gợn sóng hoặc nhăn.
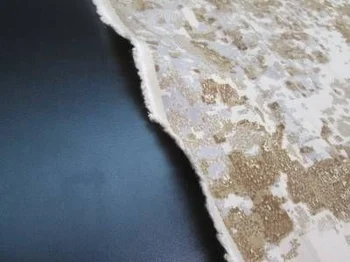
-
Nguyên nhân:
Do điều chỉnh máy dệt không đúng và cấu tạo mép vải không đúng cách.
-
Cách phòng ngừa:
Điều chỉnh máy dệt một cách chính xác và xây dựng mép vải đúng tiêu chuẩn kỹ thuật.
14. Snags (Lỗi móc sợi)
-
Định nghĩa:
Là hiện tượng một phần sợi bị kéo ra hoặc bị nhấc khỏi bề mặt vải, thường xuất hiện dưới dạng một vòng sợi lớn. Trong warp knits, snag xuất hiện theo hướng “wale”, còn trong weft knits, theo hướng “course”.
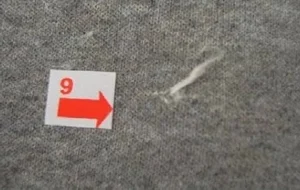
-
Nguyên nhân:
Do căng cơ học trong quá trình đan và sự xuất hiện của các vật sắc nhọn có thể gây ra hiện tượng này bất cứ lúc nào.
-
Cách phòng ngừa:
Kiểm tra các điểm tiếp xúc của vải trên máy móc để phát hiện và loại bỏ các điểm sắc nhọn. Ngoài ra, tiến hành mace snag test (kiểm tra bằng quả bóng có gai) để đánh giá khả năng chịu snag của vải.
15. Thick place/thin place (Vị trí dày/mỏng)
-
Định nghĩa:
Là hiện tượng xuất hiện các vùng vải có sợi dày (thick place) hoặc sợi mảnh, rời rạc (thin place) khác biệt so với phần lân cận.
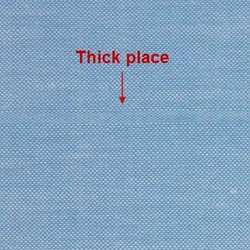
-
Nguyên nhân:
- Cung cấp sợi không đều
- Cài đặt không đúng của chốt giữ và thả trên bánh răng của cơ chế cuốn sợi
- Các bánh răng của cơ chế cuốn sợi không khớp đúng cách
- Răng bánh răng bị mòn hoặc gãy
-
Cách phòng ngừa:
Đào tạo nhân viên vận hành máy để đảm bảo quá trình cấp và cuốn sợi được thực hiện đúng cách và kiểm tra thường xuyên các thiết bị liên quan.
16. Bowing and skewing (Cong và xiên canh)
-
Định nghĩa:
Bowing là hiện tượng filling yarns bị lệch khỏi đường vuông góc với mép vải, tạo thành một đường cong; skewing là sự lệch góc (xiên canh) so với đường vuông góc với mép vải.
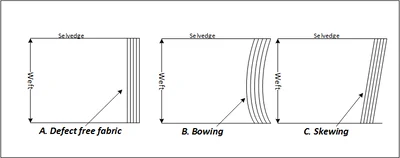
-
Nguyên nhân:
Do sự phân bố không đều của độ căng trên chiều rộng của vải trong quá trình nhuộm hoặc hoàn thiện, hoặc do việc kéo căng không đúng cách trong quá trình scouring, nhuộm hay finishing.
-
Cách phòng ngừa:
Điều chỉnh lại các cài đặt độ căng trên máy móc hoặc xử lý vải qua máy ép, làm thẳng để khắc phục lỗi này.
17. Needle lines (Vết kim)
-
Định nghĩa:
Là các vệt dọc nổi bật xuất hiện trên các loại vải đan.
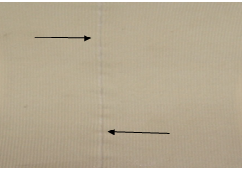
-
Nguyên nhân:
Do kim bị lỗi (kim hỗn hợp, mới, bẩn, nhiễm mảnh vụn, bẻ cong, mòn) hoặc do điều kiện không phù hợp của dial hoặc cylinder của máy móc.
-
Cách phòng ngừa:
Nếu xuất hiện từng cá nhân, truy tìm và thay thế kim lỗi; nếu xuất hiện theo dạng băng, thay thế nhiều kim. Đồng thời, đảm bảo quy trình bảo trì và làm sạch máy móc được thực hiện định kỳ.
18. Coarse pick (Sợi ngang thô)
-
Định nghĩa:
Là hiện tượng filling yarn ( sợi ngang) có đường kính bất thường lớn, còn được gọi là coarse filling hay thick filling, và thường được phân loại là lỗi nghiêm trọng.
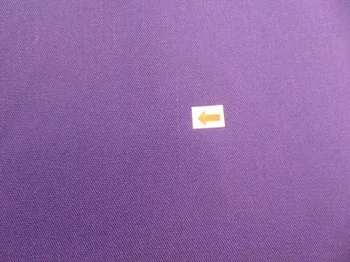
-
Nguyên nhân:
Có thể do:
- Quấn đầu sợi gãy với đầu sợi liền kề tại khung xoắn
- Trọng lượng của các con lăn phía sau bị xáo trộn, khiến vật liệu trượt dưới con lăn và làm gấp sợi dày
-
Cách phòng ngừa:
(Bản gốc không có hướng dẫn phòng ngừa cụ thể.)
19. Coarse end (Sợi dọc thô)
-
Định nghĩa:
Xảy ra trên vải có sợi dọc khi đầu sợi có đường kính lớn hơn bình thường (đôi khi gấp đôi), trái ngược với fine end (đầu sợi mảnh). Đường kính quá lớn, không đều hoặc chứa vật liệu lạ cản trở việc tạo ra vải mịn màng.
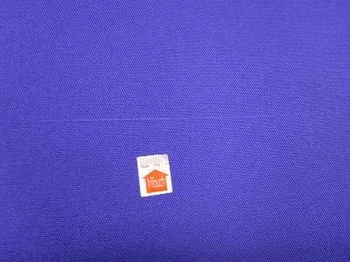
-
Nguyên nhân:
Do hai bobbin của sợi roving chạy cùng nhau trong quá trình quay (doubling) nhằm loại bỏ sự biến đổi về độ dày.
-
Cách phòng ngừa:
Đảm bảo rằng sợi roving không có nút thắt, sự không đều hay vật liệu lạ trước khi tiến hành doubling.
20. Broken pick (Đứt sợi ngang )
-
Định nghĩa:
Là sự gián đoạn rõ ràng trong mẫu dệt của sợi ngang do sợi bị gãy hoặc cắt, dẫn đến việc chèn vào vải một phần mũi chảy.
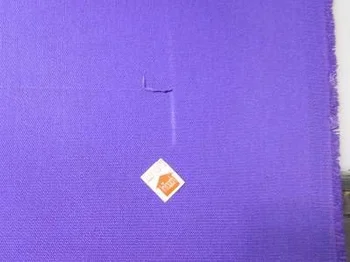
-
Nguyên nhân:
Xảy ra sau weft break, weft exhaustion hoặc do lỗi trong cơ chế weft fork.
-
Cách phòng ngừa:
Điều chỉnh chuyển động dừng của sợi ngang (weft stop motion) và đào tạo nhân viên để phát hiện, thay thế sợi bị đứt kịp thời.
21. Broken end (Đứt sợi dọc)
-
Định nghĩa:
Là khuyết điểm khi đầu sợi dọc bị gãy và không được buộc lại, thường xuất hiện dưới dạng các đường ngang cách đều nhau trên vải.
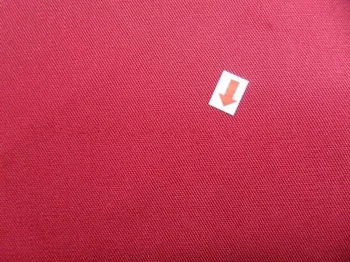
-
Nguyên nhân:
Do sợi bị đứt trong quá trình dệt hoặc hoàn thiện, có thể do chuẩn bị không tốt, sợi yếu hoặc độ căng sợi dọc quá mức.
-
Cách phòng ngừa:
(Bản gốc không có hướng dẫn phòng ngừa cụ thể, tuy nhiên kiểm soát chặt chẽ quá trình dệt và hoàn thiện sẽ giúp hạn chế sự đứt sợi.)
22. Missing end/end out (Lỗi thiếu sợi dọc)
-
Định nghĩa:
Là khuyết điểm xuất hiện trên vải dưới dạng một vết nứt mỏng theo hướng sợi dọc, thường ở mép vải, và được phân loại là lỗi nghiêm trọng.
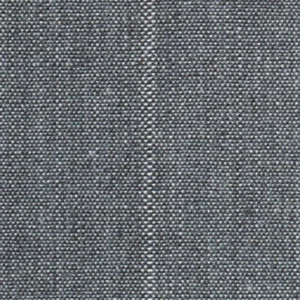
-
Nguyên nhân:
Xảy ra khi một miếng sợi thừa bị cánh bướm giật vào vải do một sợi dọc bị gãy hoặc thiếu; có thể do người dệt không kéo các đầu sợi bị đứt về vị trí đúng hoặc do chuyển động dừng sợi không hoạt động đúng.
-
Cách phòng ngừa:
Quá trình dệt nên dừng ngay khi phát hiện sợi bị gãy để ngăn chặn việc đưa các đầu sợi thiếu vào vải.
23. Filling bar (Vệt sợi ngang)
-
Định nghĩa:
Là dải hoặc thanh chạy ngang qua toàn bộ chiều rộng của vải, trong đó số mũi chảy ít hơn so với phần còn lại, khiến khu vực đó nổi bật khác biệt.
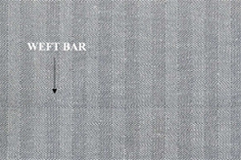
-
Nguyên nhân:
Gồm ba nguyên nhân chính:
- Các quá trình quay sợi lỗi gây ra sự biến đổi về số lượng sợi ngang
- Sự trộn lẫn của các loại sợi có số lượng hoặc độ xoắn khác nhau
- Lỗi trong cơ chế cuốn sợi trên máy dệt
-
Cách phòng ngừa:
Đảm bảo rằng nhà cung cấp có các quy trình kiểm soát và tổ chức phù hợp để loại bỏ nhầm lẫn, đồng thời duy trì hoạt động đúng của máy móc quay sợi và máy dệt thông qua bảo trì định kỳ.
FAQs: Các câu hỏi thường gặp
Lỗi vải là gì? Các loại lỗi vải thường gặp nhất?
Lỗi vải là khuyết điểm xuất hiện trong quá trình dệt, nhuộm, in hoặc gia công vải. 5 lỗi phổ biến nhất: vệt ngang, lỗ thủng, sợi đứt, nhuộm loang, vải vênh.
Cách kiểm tra chất lượng vải trước khi sản xuất?
-
Bước 1: Quan sát dưới ánh sáng để phát hiện vệt ngang, lỗi dệt.
-
Bước 2: Kéo căng vải kiểm tra độ đàn hồi, sợi đứt.
-
Bước 3: Dùng tiêu chuẩn 4 điểm (4-point system) để đánh giá mức độ lỗi.
Nguyên nhân vải bị lỗi dệt ngang? Cách khắc phục?
Nguyên nhân:
-
Máy dệt dừng đột ngột → Tạo vệt ngang (horizontal lines).
-
Sợi ngang kém chất lượng → Gây sợi thô (coarse pick).
Cách khắc phục: Bảo trì máy dệt, thay sợi định kỳ.
Vải bị lỗi nhuộm màu không đều phải làm sao?
-
Nguyên nhân: pH thuốc nhuộm sai, vải nền bẩn.
-
Giải pháp: Sử dụng chất tạo đều màu, kiểm tra vải trước nhuộm.
Tiêu chuẩn AQL trong kiểm tra vải là gì?
AQL (Acceptable Quality Level) là mức chất lượng chấp nhận được. Ví dụ:
-
AQL 2.5: Cho phép ≤2.5% lỗi trên tổng lô vải.
-
AQL 4.0: Áp dụng cho hàng giá rẻ, cho phép lỗi cao hơn.
Cách xử lý vải bị dính dầu, vết bẩn trong sản xuất?
-
Bước 1: Cách ly vải bẩn, tránh lây lan.
-
Bước 2: Dùng dung dịch tẩy chuyên dụng (không chà xát mạnh).
-
Bước 3: Sấy khô ở nhiệt độ thấp.
Vì sao vải bị co rút sau khi giặt? Có phải lỗi vải không?
Lỗi vải ảnh hưởng thế nào đến giá thành sản phẩm?
Cần làm gì khi phát hiện vải bị lỗi trong sản xuất?
-
Ngừng ngay lô vải bị lỗi, phân loại riêng.
-
Xác định nguyên nhân (máy móc, con người, nguyên liệu).
-
Đánh giá mức độ ảnh hưởng để quyết định sửa chữa hoặc loại bỏ.
Tiêu chuẩn nào dùng để đánh giá chất lượng vải?
Tiêu chuẩn phổ biến nhất là Hệ thống 4 điểm (4-point system) của AATCC/ISO, dựa trên:
Đơn vị nào kiểm tra vải uy tín tại Việt Nam?
Các công ty kiểm định được ISO/IEC 17025 công nhận:
-
Intertek, SGS, TÜV Rheinland.
-
Chi phí: ~5-10 triệu/lô tùy quy mô.
Kết luận:
Việc hiểu rõ từng loại khuyết điểm sẽ giúp chúng ta phòng tránh và cải thiện được chất lượng sản phẩm. Trước khi sản xuất, hãy thiết lập mức sai số cho các lỗi vải trong danh sách kiểm tra QC và áp dụng hệ thống nhận diện, phân loại lỗi một cách thống nhất để hạn chế tranh chấp với nhà cung cấp. Nếu gặp phải nhiều khiếu nại về chất lượng, cân nhắc thuê công ty kiểm tra bên thứ ba để đảm bảo sản phẩm luôn đạt tiêu chuẩn của công ty và đáp ứng mong đợi của khách hàng.
Bài viết gốc ở đây
|